Comprehensive Rough-In Electrical Inspection Guide
Understanding the requirements for electrical inspections is crucial for ensuring your home or project adheres to safety standards and building codes. Missed inspections can necessitate engineer letters or additional assessments. For further guidance or assistance with electrical inspections or obtaining engineer letters, Oasis Engineering is here to help.
Oasis Engineering
12/5/20234 min read
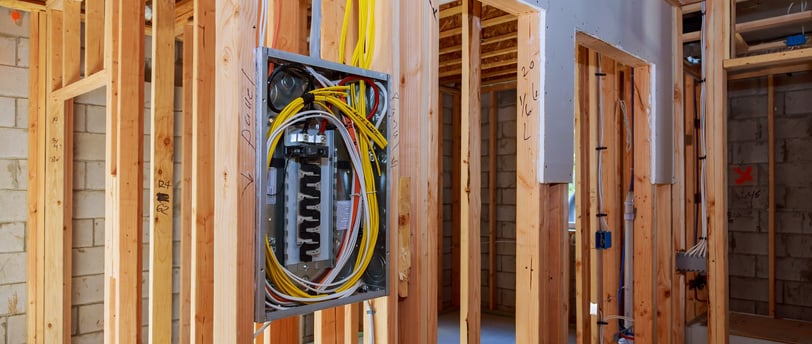
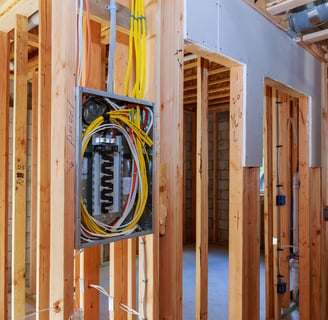
Electrical inspections are critical for ensuring the safety and compliance of electrical systems in both new constructions and remodeling projects. For your project success, these inspections are integral to adhering to building codes. This guide offers a detailed overview of what to expect during electrical inspections and provides a checklist to help homeowners and professionals prepare for them.
Two Rounds of Electrical Inspection
Rough-In Inspection: This initial inspection occurs once all electrical boxes, cables, conduit, and wires are installed, but before the walls are closed up. It allows the inspector to have a clear view of wire runs from the service panel to fixtures and appliances.
Final Inspection: Conducted when the house is complete, but before occupancy. At this stage, all walls should be closed in, painting finished, and circuits functioning.
What Inspectors Look For
Proper Circuits: Ensuring the property has the correct number of circuits for electrical demand, with dedicated circuits for certain appliances.
GFCI and AFCI Protection: Compliance with requirements for GFCI (Ground Fault Circuit Interrupter) and AFCI (Arc-Fault Circuit Interrupters) protection.
Electrical Boxes: Inspection of boxes for size, secure fastening, and flush alignment with walls.
Box Heights: Verification of consistent outlet and switch heights.
Cables and Wires: Inspection of cable clamping, wire gauge appropriateness, and wire length extending from boxes.
Cable Anchoring: Checking for proper cable anchoring to wall studs.
Wire Labeling and Surge Protection: Ensuring wires are labeled according to local codes and recommending surge protection for sensitive devices.
Common Required Rough - in Electrical Inspections Checklist - Summary
Building Permit Verification: Ensuring the permit matches the project and previous inspection records.
Wiring Methods: Checking cable assemblies for support and suitability.
Protection Against Physical Damage: Verifying cable installation clearance or protective steel plates.
Outlet Boxes: Assessing boxes for suitability of use.
Accessibility of Boxes and Conduit Bodies: Checking for easy access to junctions, outlets, and pull points.
Conductor Fill in Boxes: Ensuring compliance with conductor fill regulations.
Flush-Mounted Installations: Verifying positioning of boxes against combustible and noncombustible surfaces.
Splicing Devices and Equipment Grounding: Inspecting for correct splicing devices and equipment grounding conductors.
Kitchens, Dining Rooms, Bathrooms, and Other Rooms: Checking for appropriate receptacle spacing and dedicated circuits.
Hallways and Stairways: Ensuring proper lighting and switch placements.
Closets: Checking clearances between luminaires and storage spaces.
Laundry Area and Basements: Verifying the presence of required receptacle outlets and dedicated circuits.
Garages: Ensuring at least one receptacle outlet per bay and proper lighting.
Outdoor Requirements: Checking for exterior receptacle outlets and lighting at entrances or exits.
Service and System Grounding: Reviewing the service load, grounding electrodes, and main bonding jumpers.
Feeders and Panelboards: Verifying proper sizing, ratings, accessibility, and clearances around panelboards.
Understanding the requirements for electrical inspections in your city or county is crucial for ensuring your home or project adheres to safety standards and building codes. Missed inspections can necessitate engineer letters or additional assessments. For further guidance or assistance with electrical inspections or obtaining engineer letters, Oasis Engineering is here to help.
Rough-In Electrical Inspection Checklist for Effective Compliance
General Areas
Building Permit and Plans: Ensure the building permit and approved set of plans are available and match the route card.
Wiring Methods: Check cable assemblies for support and suitability according to NEC Chapters 3, 7, and 8.
Protection Against Physical Damage: Verify 1 1/4-in. clearance or protective steel plates for cable installation through or parallel to framing members (NEC 300.4).
Outlet Boxes: Assess boxes for suitability of use (NEC 314.27) and ensure they are installed in accessible locations (NEC 300.15, 314.29).
Box Security: Confirm that cables are secured to boxes (NEC 314.17 B and C).
Conductor Fill: Check the number of conductors in outlet, device, and junction boxes for compliance with NEC 314.16.
Flush-Mounted Installations: Ensure proper positioning of boxes against finished surfaces (NEC 314.20).
Equipment Grounding and Bonding: Inspect splicing devices and bonding connections (NEC 250.8, 250.86, 250.146, 250.148).
Grounding Conductors: Verify suitability and size (NEC 250.118, 250.122).
Temperature Recessed Luminaires: Check for clearances from combustibles and insulation (NEC 410.115, 410.116).
Bonding Metal Pipe Systems: Ensure compliance (NEC 250.104 B).
Smoke Detectors: Confirm spacing, interconnection, and arch fault protection (NFPA 72, FBC 907, 908.7, 603, R315, NEC 210.12 A).
Fire Walls: Check boxes for compliance (NEC 300.21).
Ceiling Fan Support: Verify support for fan boxes (NEC 314.27 C, 422.18).
Kitchen
Receptacle Spacing: Check receptacle spacing for walls, countertops, and work surfaces (NEC 210.52 A and C).
Branch Circuits: Ensure a minimum of two 20-A small-appliance branch circuits (NEC 210.52 B).
Lighting Outlet: Verify the presence of a wall-switched lighting outlet on a general circuit (NEC 210.70 A, 210.52 B 2).
Appliance Circuits: Check for correctly sized circuits for specific appliances (NEC 210.23, 422.10).
Additional Branch Circuits: Confirm the presence of extra small-appliance branch circuits for multiple kitchens (NEC 210.52 B 3).
Dining Room
Receptacle Outlets: Ensure proper spacing and that they are supplied by small-appliance branch circuits (NEC 210.52 A, B).
Lighting: Confirm wall-switch-controlled lighting on a general lighting circuit (NEC 210.70 A, 210.52 B 2).
Bathrooms
Receptacle Outlets: Check that receptacles are adjacent to basins and on dedicated circuits (NEC 210.52 D, 210.11 C 3).
Lighting Outlet: Confirm the presence of wall-switch-controlled lighting on a general circuit (NEC 210.70).
Other Habitual Rooms and Hallways
Receptacle and Lighting Outlets: Ensure proper spacing and wall-switch-controlled lighting outlets (NEC 210.52 A, NEC 210.70).
Stairways and Closets
Lighting Requirements: Verify lighting outlet requirements for stairways (NEC 210.70 (A) (2)) and clearances for closets (NEC 410.2, 210, NEC 410.16).
Laundry Area
Receptacle Outlet: Ensure at least one receptacle outlet is installed (NEC 210.52 (F)) and that it is supplied by a dedicated 20-A circuit (NEC 210.11 (C) (2)).
Basements, Attics, and Garages
Receptacle and Lighting Requirements: Verify receptacle outlets and lighting requirements in these areas, adhering to NEC standards.
Outdoors
Receptacle and Lighting Outlets: Ensure compliance with outdoor electrical requirements per NEC 210.52 (E), 210.63, NEC 210.70 (A) (2).
Services and System Grounding
Service Load and Conductors: Review service load calculations and ensure conductors are properly sized (NEC Article 220, 230.42).
Service Disconnects and Grounding: Verify service disconnect locations and grounding requirements (NEC 230.70, 230.91, 250.50, 250.52).
Feeders and Panelboards
Ampacity and Panelboards: Check feeder loads, conductor sizing, and panelboard requirements (NEC Article 220, 310.15, NEC 110.26, 240.24).
This comprehensive checklist is designed to cover all critical aspects of a rough-in electrical inspection, ensuring each element is scrutinized for compliance with the NEC and other relevant standards. It serves as a detailed guide for inspectors, electricians, and homeowners to prepare for project success.